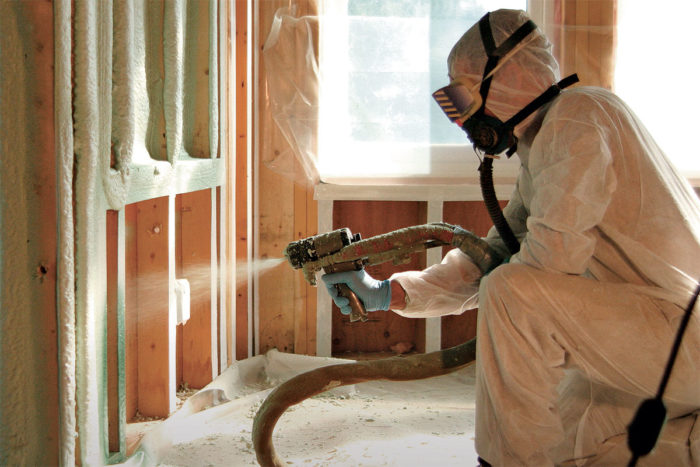
According to the International Organization for Standardization (IOS) the term is too vague to be meaningful. The US Environmental Protection Agency (USEPA) agrees, but only to a point. The USEPA created the international Energy Star program in an attempt to provide the manufacturers of goods with a voluntary labeling system for promoting energy efficient products.
In the 1990’s when the program was started, it was only applied to appliances and electronics. However, today entire homes and home offices are able to gain Energy Star certification. The only criteria is the building must use 15% less energy than a standard home built to the 2004 International Residential Code. How does a home achieve that rating? The things at the top of the list for getting an Energy Star rating are not surprising: insulation, high performance windows, tight construction and ducting, energy efficient cooling and heating systems and Energy Star certified products (appliances, lighting, water heaters).
Now, in reference to insulation specifically, its efficiency is measured according to R-value. An R-value is a mathematical calculation which produces the level of thermal resistance a building has. For the average North American home insulated with traditional fiberglass batts, R-value sits at between 3.1 and 4.3 per square inch. Blown in fiberglass insulation has a typical R-value between 2 and 4 per square inch. According to the US Department of Energy, the same home insulated with spray foam polyurethane insulation will have an R-value between 7 and 8 per square inch. Clearly a home insulated with spray foam would be well on its way to achieving an Energy Star rating, even without installing LED lighting and thermal windows.
When a building is insulated with polyurethane foam, the costs of heating and cooling will undoubtedly be vastly reduced. Many spray foam manufacturers report that energy costs can be reduced by up to 40%; a claim that is both highly likely and easily attainable. With such a diminished use of energy, there is less demand for petroleum-based products and fossil fuels, resulting in a smaller carbon footprint being left on our planet.
We are halfway to answering our title question, is spray foam insulation really green? Now we know its immense potential for energy savings, but what about the manufacture of the foam itself? In the case of spray foam, the two substances that come together to produce the foam must remain separate until the time of application. Those two things are polyol (a naturally occurring alcohol) and diisocyanate (a group of organic compounds derived from plant and animal materials). When they are brought together with water, an exothermic reaction takes place producing the polyurethane foam. Although the foam is produced from organic substances, it does not breakdown over time – a good thing for insulation applications, but where does it go when it is no longer needed?